Filtration
Filtration: Definition, Objective, Application, Principle, Construction and Working of Membrane Filter and Sintered Glass Filter.
PHARMACEUTICS
Alok Bains
11/3/20236 min read
Filtration
Filtration is a process of separating insoluble solid particles from liquid or gas by passing them through a porous medium. A porous medium is called filter media that retains solid and allows fluid to pass through it. A mixture containing insoluble solid particles and liquid is called a slurry. The fluid obtained after filtration is called filtrate. Solid retained by filter media is called filter cake. Separation of coarse particles from slurry by using muslin cloth or cotton wool is called straining.
Removal of insoluble particles from slurry containing less than 1% insoluble particles is called the clarification process. The separation of insoluble particles from the fluid by passing it through the porous medium under pressure is called ultra-filtration.
Principle/Theory of filtration: Filter medium retains insoluble solid as filter cake and liquid to pass as filtrate. This filter cake also retains insoluble particles and is called a Secondary filter medium. In fact, secondary filter media is more efficient than primary filter medium. The theory of filtration states some factors affect the rate of filtration. The theory of filtration can be expressed by Darcy’s Law. Darcy’s law is expressed by following the equation
dV/dt = KAΔP/ηl.
dV/dt = Rate of filtration,
· V: Volume of filtrate
· t: time of filtration
· K: Constant. It is the permeability coefficient of filter media and filter cake.
· A: Area of filter media.
· ΔP: Pressure difference between above filter media and below filter media.
· η: Viscosity of fluid
· l: Thickness of filter bed (filter cake + filter media).
Factors affecting filter media
Darcy’s Law states that the following factors affect the rate of filtration
1. Surface area of filter medium: The rate of filtration is directly proportional to the surface area of filter medium. The rate of filtration increases as the surface area of the filter medium increases. In the laboratory pleated filter paper is used as a filter medium. Pleated filter paper increases the surface area for filtration.
2. Pressure difference: The rate of filtration is directly proportional to the pressure difference between pressure above the filter medium and pressure below the filter medium. The rate of filtration can be increased by increasing the pressure above the filter medium or by decreasing the pressure below the filter medium. Pressure below the filter medium can be decreased by creating a vacuum below the filter medium. But this pressure difference should be under the limit. It may rupture the filter medium.
3. Viscosity: The rate of filtration is inversely proportional to the viscosity of the liquid. The rate of filtration decreases as the viscosity of the liquid increases. The viscosity of a liquid can be decreased by increasing the temperature of the liquid to be filtered.
4. Thickness of filter medium: The rate of filtration is inversely proportional to the thickness of the filter medium. Filter cake acts as a secondary filter medium. Thus as the thickness of the filter cake increases during filtration, there will be a decrease in the rate of filtration.
Apart from these factors expressed in Darcy’s equation, the following factors also affect the rate of filtration.
5. Pore size of filter medium: The rate of filtration is directly proportional to the pore size of the filter medium. The rate of filtration of slurry containing fine solid particles is very slow due to the very small size of pores in the filter medium.
6. Temperature: The rate of filtration is directly proportional to the temperature of the slurry. An increase in temperature decreases the viscosity of slurry. This increases the rate of filtration.
7. Nature of insoluble solid: Some insoluble solid forms hard filter cake. Some insoluble solid forms porous cake. Rate filtration shall be high for solid-forming porous cake.
Rate of filtration = Area of filtration X Pressure difference/ Viscosity X Resistance of filtration medium and filter cake.
MEMBRANE FILTRATION
Membrane filtration is a method to separate particles or molecules from fluid (liquid or gas) by using a membrane filter. A membrane filter is also known as a molecular filter or biological filter. It is about 150 µm thick and contains millions of micropores of uniform size. Pire size is either 0.22 µm or 0.45 µm in diameter. It is used to remove microorganisms, particulate matter, and organic materials which impart color, taste, and odor to liquid.
A. Principle: Membrane filtration separates solids from liquid or gas by applying driving force across the filter membrane. Filter membranes retain solid particles by mechanical retention, adsorption retention, bridging retention, and network retention.
1. Mechanical retention: The filter membrane retains solid particles with particle sizes larger than the pore size of the filter membrane. It is considered as screening.
2. Adsorption retention: It is the physical retention of solid particles. Filter membrane adsorbs solid particles by using electrostatic charges on solid particles. Solid particles smaller than the pore size of the filter membrane are retained by this mechanism.
3. Bridging retention: Solid particles smaller than the pore size of the filter membrane are trapped inside the pores of the filter membrane. This is called bridging retention.
4. Network interception: Solid particles are retained inside the filter membrane in place of the upper side of the filter membrane.
B. Construction: Membrane filtration is carried out by using a membrane filter unit also called membrane filtration assembly. On a laboratory scale, it consists of a funnel, locking rings, carbon disc, rubber stopper, filter flask, vacuum pump, and stainless steel base. The funnel is located at the top of the filter membrane assembly. The base of the funnel has A locking ring. It controls the flow of liquid during filtration. The stainless steel base has a carbon disc and a filter membrane on the carbon disc. A stainless steel base is present in between the funnel disc and filter flask. The filter flask has an outlet to be connected to the vacuum pump.
Depending upon the pore size of the filter membrane, membrane filtration is of the following three types’ microfiltration, ultrafiltration, nanofiltration, and reverse osmosis process. This membrane filtration works under pressure differences across membrane filters. This pressure difference develops a driving force across the filter membrane for filtration.
1. Microfiltration: The pore size of the membrane filter varies from 0.03 microns to 10 microns. Normally silt, sand, clay, cysts, algae, etc are filtered in microfiltration.
2. Ultrafiltration: The pore size of the membrane filter varies from 0.002 microns to 0.1 microns. It acts as a bacteria-proof filter membrane. It can remove all microorganisms from water to make water sterile.
3. Nano-filtration: The pore size of a membrane filter in nano-filtration is about 0.001 microns. It removes all microorganisms, viruses, and humic materials.
All these three filtration works under pressure difference across membrane filter. The pressure difference in ultrafiltration shall be more than in microfiltration. The pressure difference in nano-filtration shall be greater than in ultrafiltration.
4. Reverse osmosis: Filter membrane in reverse osmosis (RO) act as semipermeable membrane. It blocks all soluble salts, minerals, and other impurities. It allows only water molecules to pass through it.
C. Working: Liquid to be filtered is placed into a funnel and a vacuum is created inside the filter funnel. It develops a driving force across the filter membrane due to the vacuum in the filter funnel. It is called filtration under a negative force that sucks liquids into the funnel as filtrate.
D. Application of microfiltration:
1. In-water plant treatment: To remove protozoa from water.
2. In the pharmaceutical industry: To sterilize the solution.
3. In the dairy industry: To remove bacteria and spores from milk.
4. In microbiology: To clarify culture media.
E. Application of ultrafiltration
1. To make potable water suitable for drinking purposes
2. In the dairy industry to make protein concentrate,
3. In the dairy industry to make cheese whey,
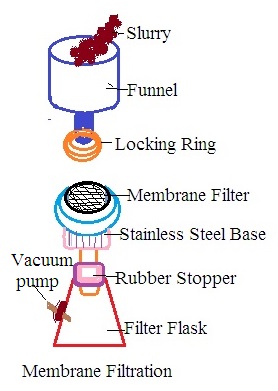
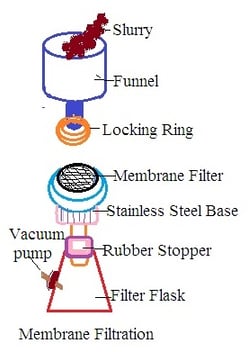
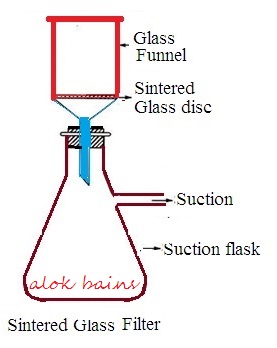
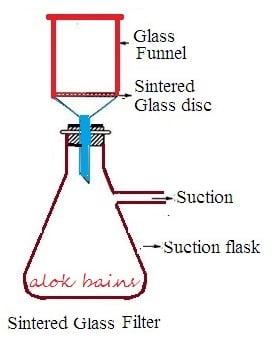
SINTERED GLASS FILTER
It is made of borosilicate glass. Borosilicate glass is finely powdered, and sieved to obtain desired size of borosilicate glass powder particles. Powdered particles are heated to melt and packed to form a disc shape. The disc is fused to a funnel of suitable shape and size. The funnel containing sintered glass is numbered. This numbering depends upon pore size.
Principal: During filtration high pressure difference is used. It filters out all insoluble constituents and bacteria present in the liquid.
Care: Sintered glass filter is made of glass filter that needs proper cleaning before and after use to remove contaminants.
1. Clean the disc with diluted hot hydrochloric acid followed by several rinsing with distilled water.
2. Wash it as quickly as possible after its use. Use a soft brush to clean all parts,
3. Scrub a soft brush gently to avoid scratching on glass parts. Rinse it thoroughly
4. Dry it at room temperature or in the oven. Do not exceed oven temperature above 100 degrees C. Above 100 degrees C, there will be damage to the sintered glass filter.
5. Do not use hot concentrated phosphoric acid or hot alkaline solution for cleaning. It decreases the life of the sintered filter and increases the size of the pores.
Working procedure: Slurry is placed in a sintered glass funnel. Pressure is applied over the funnel or a vacuum is created under the funnel to create pressure difference. Collect filtrate through the neck of the sintered glass funnel.
Use: It has good mechanical strength to filter liquids for bacteriological and cytological studies.