Tablets Manufacturing Defects
Manufacturing Defects in Tablets, Weight Variations, Hardness Variation, Tablet Sticking with Die, Capping, Lamination, Splitting, Picking and Sticking, Mottling, and Double impression.
PHARMACEUTICS
Alok Bains
12/1/20232 min read
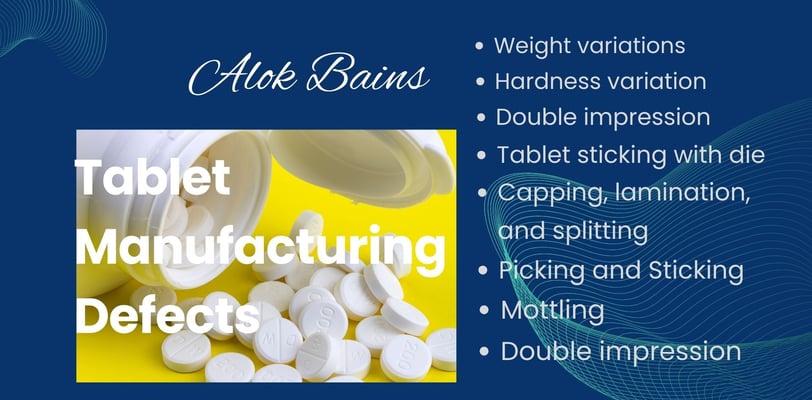
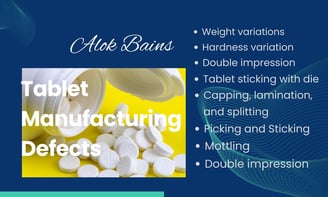
Manufacturing Defects in Tablets, Weight Variations, Hardness Variation, Tablet Sticking with Die, Capping, Lamination, Splitting, Picking and Sticking, Mottling, and Double Impression.
Manufacturing Defects in tablets
Defects in tablets may occur during the manufacturing of tablets and after the manufacturing of tablets. These defects are Tablet sticking with die, capping in tablets, splitting in tablets, picking, sticking, mottling, and double impression.
1. Weight variations:
All tablets in one batch should have uniform weight.
Reasons:
I. Variation in granule size.
II. Excess fines powders in granules.
III. Improper mixing of lubricants in granules.
IV. Improper flow of granules in tablet machine.
V. Change in capacity of dies during compression of tablets.
VI. Changes in granule compression speed.
Remedies: Controlling the size of granules, Proper lubricant mixing, and proper speed of tablet machine, helps to control weight variation in tablets.
2. Hardness variation:
Tablets will not have the same hardness. The reasons are similar to weight variation.
3. Tablet sticking with die:
Stickiness in dies may develop. This creates a characteristic noise and difficulties in tablet ejection. It makes the tablet surface rough. It is mainly due to worn-out dies, dirty dies, under-dried granules, or poor lubrication of granules.
4. Capping, lamination, and splitting:
Partial or complete removal of the top or bottom portion of a tablet is called capping of tablets. Break down of tablets into two or more pieces is called splitting of tablets. The separation of tablets into two layers is called lamination. These defects can be checked by vigorous shaking of tablets or by using a friability test apparatus.
Reasons:
1. Excessive fine powders or very less fine powders in granules.
2. Entrapment of air in tablets during compression of granules.
3. Over-drying of granules.
4. Too high or too low compression force.
5. High speed of tablet compression.
6. Wear and tear in punches and dies.
7. Wrong setting of punches regarding ejection of tablets from the die.
Remedies
1. Replacement of worn dies and punches with buffed or polished dies without any defect.
2. Proper setting of dies and punches for smooth ejection of tablets
3. Optimum quantity of fines in granules.
4. Avoid over-drying of granules and maintaining proper moisture in granules.
5. Optimum speed of granule compression into tablets.
6. Optimum compression force during compression.
5. Picking and Sticking:
Particles from the surface of tablets stick to the surface of the punch. Punch removes these particles from the tablet surface. The tablet surface will become rough.
Reasons:
I. Defective dies and punches.
II. Small amount of lubricants in granules.
III. Moist granules.
IV. Excess amount of fine powders in granules.
V. Improper ratios of ingredients tablet formulation.
Remedies:
I. Use of a new set of dies and punches.
II. Use the correct amount of lubricant
III. Properly dried granules.
6. Mottling:
The uneven coloration of tablets is called mottling. It occurs mainly in colored tablets due to the uneven distribution of coloring agents in tablets.
Reasons:
I. Dye migration in granules during granules drying.
II. Different coloration of excipients.
Remedies
I. Granules drying at low temperatures.
II. Use of dye to mask the color of all excipients.
7. Double impression:
Tablets with monograms or any other engraved mark may have double impressions. Punch compresses granules twice during compression of granules. It is due to slight free movement in punches during compression. Punch rotates slightly during its free travel while compressing granules. This defect can be removed by controlling the movement of the punch during compression.
Alok Bains