Tablet coating
Tablet coating Advantages, Disadvantages, Types of Tablet Coating, Sugar Coating, Film coating, Enteric Coating, Micro Encapsulation.
PHARMACEUTICS
Alok Bains
11/30/20235 min read
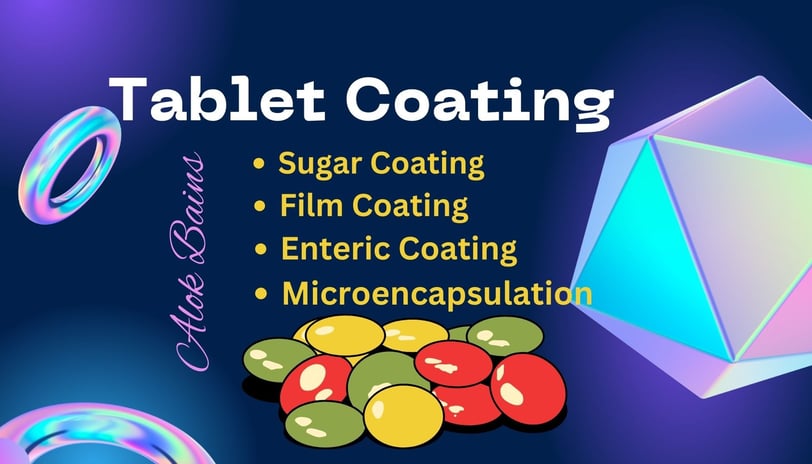
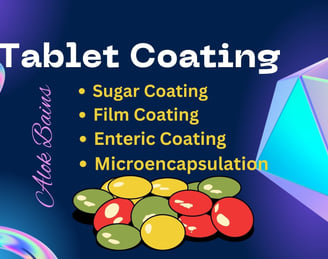
Tablet coating Advantages, Disadvantages, Types of Tablet Coating, Sugar Coating, Film Coating, Enteric Coating, Micro Encapsulation.
Tablet coating
Tablet coating is a process of applying a thin layer of substances on the surface of a compressed tablet. The main aims of tablet coating are (Advantages):
1. To improve the appearance, texture, and elegance of tablets.
2. To improve organoleptic (Colour, taste, and flavor) properties of tablets.
3. To mask the unpleasant odor and taste of medicaments.
4. To improve the stability of tablets.
5. To protect the medicaments of tablets from air, moisture, and light.
6. To delay or prolong the release of medicaments from tablets.
7. To control the release of drugs at a particular site in GIT.
Disadvantages of tablet coating
1. Increase in thickness of tablets.
2. Weight variation in tablets.
3. Decreased disintegration and dissolution rate of tablets.
4. Delay in release of medicaments from the tablets.
5. Increase in reduction cost of tablets.
6. Chance of allergy to patients
7. Interaction of film coating materials, and tablets ingredients.
Types of tablet coating
There are several types of tablet coating such as sugar coating, film coating, enteric coating, and Microencapsulation,
1. Sugar coating
coating masks the unpleasant taste and odor of medicaments, and protect tablets from external environment such as air, moisture, and light. It also improves the elegance, texture, and appearance of tablets. It is easier to apply a sugar coat on convex tablets than on flat tablets. The following steps are followed in the sugar coating of tablets.
a. Sieving: Shake tablets on a suitable sieve to remove fine particles present on tablets.
b. Sealing: Sugar dissolved in water is used for the sugar coating of tablets. This water may damage the tablet during sugar coating. Thus one or two water-proof layers are applied on tablets before sugar coating. Arsenic-free Shellac or cellulose acid phthalate solution in alcohol or acetone is used as water-proof material to protect tablets from water during sugar coating.
Put water-proof coating solution into the coating pan. Put tablets to be sugar-coated into the pan. Rotate the coating pan by using an electric motor and blow hot air into the coating pan. Rotate the rotating pan at a speed that stops tablets from sticking to each other. Remove coated tablets from the rotating pan and allow them to dry in the air.
Repeat this process by applying several layers of sugar coat on the tablet till the required thickness of the tablets. Remove the coated tablets from the pan and allow them to dry in the air.
d. Smoothing: Apply another coat of heavy sugar on subcoated tablets and simultaneously dry it. Repeat this process till the tablet's surface becomes smooth and tablets of the required size are manufactured.
e. Colouring: Water soluble and FDA-approved coloring agents are used to color sugarcoated tablets. Dissolve color in dilute syrup. Apply color coat by using the same procedure discussed under the above steps of coating to produce uniform color in all tablets.
f. Polishing: Dissolve beeswax in a suitable volatile organic solvent. Put dried sugar-coated tablets into a canvas drum (polishing pan). Rotate the polishing pan by using an electric motor. Add beeswax solution. Allow the sugar-coated tablet to rotate till all solvent evaporates from the polishing pan. This step develops shining on sugar-coated tablets.
Film coating: Film coating develops a waterproof layer on tablets. It does not produce tablets as elegant as sugar coating. But it saves lots of time and labor to coat tablets. It does not require several steps such as sealing, sub-coating, and smoothing.
Advantages of film coating:
1. Low labor cost.
2. Low material cost.
3. One-step procedure.
4. Less time-consuming procedure.
5. No adverse effect on tablet ingredients.
6. Protection from moisture during storage of tablets.
7. Not much increase in tablet weight.
8. Resistant to cracking and chipping.
9. Improve elegance and mask tablet defects.
Enteric Coating
Enteric coating of tablets ensures the disintegration of tablets in alkaline media not in acidic media. Enteric-coated tablets disintegrate in small intestine not in the stomach inside GIT. Enteric coating is carried out under the following conditions:
1. Medicaments that develop irritation in the stomach are dispensed as enteric-coated tablets.
2. Medicaments sensitive to acid are dispensed as enteric-coated tablets.
3. Medicaments to be absorbed from the intestine are dispensed as enteric-coated tablets.
4. Medicaments to produce action in the intestine are dispensed as enteric-coated tablets.
5. Medicaments action to be delayed is dispensed as enteric coated tablets.
Enteric coating materials such as a solution of salol, cellulose acetate phthalate, shellac, and shellac derivatives in volatile organic solvents are used for the enteric coating of tablets. Among them, cellulose acetate phthalate is most commonly used as it gives the most satisfactory result.
Put tablets into the rotating pan. Spray enteric coating materials dissolved in volatile organic solvents such as acetone or alcohol. Blow hot air to evaporate the solvent. A fine coat of enteric coating material will develop on tablets. The process is continued till a uniform layer of enteric coating materials develops on tablets.
Microencapsulation:
A thin coating of solid particles or liquid droplets or dispersed globules to form microcapsules is called microencapsulation. Particles may be single or clusters of particles. There are several techniques for microencapsulation such as pan coating, Fluidised bed coating, Coacervation, Electrostatic deposition, Vacuum deposition, Polymerization, and Multi-orifice centrifugal process. Materials for coating are gelatin, polyvinyl alcohol, ethyl cellulose, cellulose acetate phthalate, etc.
1. pan coating: It is suitable for particles larger than 600 µm. Particles are coated with sugar in a coating pan to form spherical pellets. Dissolve coating material in a suitable volatile organic solvent. Spray it on pellets rotating inside the coating pan. Blow hot air to dry it. Continue the process to get the required thickness of the coating.
2. Fluidized bed coating: Dissolve coating materials in a suitable volatile organic solvent. Place solid particles to be coated in a fluidized bed dryer under a blow of hot air. Spray coating materials solution of floating solid particles. Allow coated particles to dry. Coated particles will become heavy and fall down near the outlet. Thickness coating will depend upon the size of solid particles, viscosity of coating material solution, air velocity, and hot air temperature.
3. Coacervation: The separation of two hydrophilic colloids present in a mixture is called coacervation. It separates both liquid phases. Dissolve coating materials in a suitable solvent. Disperse solid particles in coating materials solution. Allow coating materials to settle down on sold particles. Remove solvents by using a suitable technique. Free-flowing coated particles shall be available.
4. Electrostatic deposition: It is used to coat both solid particles and liquid droplets. Apply electric charges on both coating materials and solid particles/droplets. Place charged solid particles/droplets into the coating chamber. Spray charged coating materials on charged solid particles/droplets. Both have opposite charges, thus coating materials will get deposited on solid particles/droplets.
5. Vacuum deposition: Mix coating materials solution with solid particles. Evaporate solvent under vacuum. It will form coated pellets.
6. Polymerization: Monomer is used as coating material. It is mixed with the core materials. Polymerization occurs to form a coat over solid particles.
7. Multi-orifice centrifugal process: It is the mechanical process of microencapsulation. Both solid and liquid can be encapsulated by this method. Materials to be encapsulated are passed through coating materials under centrifugal forces. This results encapsulation of materials.
Alok Bains