Size Separation
Size separation: Classification of Powders according to IP, Cyclone Separator, Sieves, and Standards of Sieves.
PHARMACEUTICS
Alok Bains
10/23/202311 min read
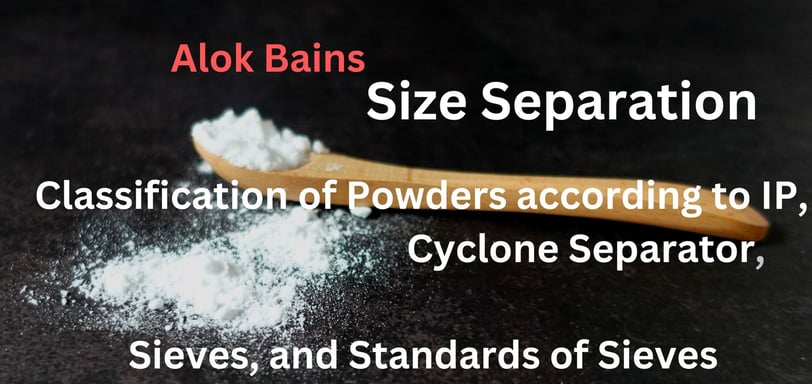
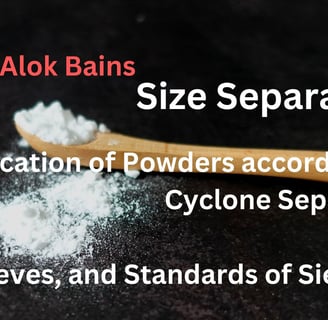
SIZE SEPARATION (Sieving, screening, or shifting): Objectives, applications & mechanism of size separation, official standards of powders, sieves, size separation Principles, construction, working, uses, merits and demerits of Sieve shaker, cyclone separator, Air separator, Bag filter & elutriation tank
SIZE SEPARATION (Sieving, screening, or shifting)
Objectives (Aims)/Application: Size reduction cannot produce powders of uniform particle size. Ideally, powders should have uniform particle size. Size separation is carried out.
1. To separate powder particles as per their particle sizes.
2. To measure the size of particles in powder.
3. To produce precise dosing and quality formulation
4. To optimize crushing, grinding, or mixing, and reduce energy consumption
5. To analyze the quality of raw materials
6. To test the efficacy of size reduction mills
7. To select a sieve system for size reduction mill.
Definition: “Size separation in a unit operation to separate powder particles of various sizes into two or more parts having approximately similar particle size.”.
Mechanism of Size separation: Size separation can be achieved through various mechanisms. It depends on the characteristics of the materials being separated and the specific requirements of the process. The following are some common mechanisms of size separation:
1. Sieving: It is one of the simplest and most widely used methods for size separation. It involves the passing of powder particles through a sieve or screen with a specific size of mesh. Larger particles are retained on top of the sieve, while smaller particles pass through. Sieving is carried out by agitation, brushing, or centrifugation.
Agitation: Oscillation, vibration, or gyration are used to agitate the powder bed on the sieve. Back and forth movement of the sieve is called oscillation. Powder particles move parallel to the sieve during oscillation. The inclination of the sieve during sieving increases the efficiency of the sieve. Vibration is repetitive rapid movement from one position to another position. Rapid vibration forces particles to pass through the sieve mesh. The flywheel gives a rotary motion to the sieve. The rotary motion of the sieve develops a spinning motion in the powder particles. Particles pass through a sieve mesh during spinning. This is gyration. The gyratory motion also develops vibration that bounces the powder particles against the sieve surface.
Advantages of the Agitation method: Inexpensive, simple, and rapid.
Disadvantages:
· Powder should be dry. The moist powder will stick to the sieve.
· Agitation develops attrition. That will further reduce the particle size.
Brushing: A brush rotates on the sieve to keep the sieve mesh clear. It is useful for greasy and sticky powder particles. It prevents mesh clogs.
Centrifugation: It is used in the vertical cylindrical sieves. The high-speed rotors rotate the vertical sieve at a very high speed that generates centrifugal force in the particles to pass through the vertical sieve mesh.
2. Gravity separation: Gravity settles down the solid particles in the fluid medium. The rate of settling velocity depends upon the size and density of the particles. Larger and heavier particles settle down at a faster rate than the smaller and lighter particles. This develops distinct zones in a column depending on particle size. Sedimentation and hydrocyclones work on this mechanism. in the
3. Gravity Separation: Gravity separation relies on the differences in the settling velocities of particles in a fluid medium (such as air or water) to separate them based on size. In gravity separation methods such as sedimentation or hydrocyclones, larger and heavier particles settle faster than smaller and lighter particles, leading to the formation of distinct size fractions.
4. Centrifugation: Centrifugation involves spinning a mixture of particles at high speeds in a centrifuge. The centrifugal force generated causes particles to separate based on their size and density. Larger and denser particles move towards the outer edge of the centrifuge tube while smaller and lighter particles remain closer to the center.
5. Filtration: Filtration is a size separation technique that involves passing a mixture of particles through a porous medium. The porous medium selectively retains particles based on their size, allowing smaller particles to pass through while larger particles are retained.
6. Magnetic separation: Magnetic separation utilizes the magnetic properties of certain materials to separate them from a mixture based on size. Magnetic separators apply a magnetic field to the mixture, causing magnetic particles to be attracted to the magnetic surface while non-magnetic particles are unaffected and can be separated from the mixture.
7. Floatation: Flotation separates on the basis of size and density of the powder particles. In flotation, particles are selectively attached to air bubbles and carried to the surface of a flotation cell, where they can be collected as a froth concentrate, leaving the remaining particles behind.
8. Electrostatic: Electrostatic separation utilizes differences in the electrical conductivity or surface charge of particles to separate them based on size. In electrostatic separators, particles are charged by passing them through an electric field, causing them to be attracted or repelled based on their charge, size, and surface properties.
Sieves and standard of sieves:
“Pharmacopoeial sieves have a square mesh of uniform size made up of rust-proof metallic wires as woven material.” Normally, metallic wires of brass, bronze, or stainless steel are used in pharmacopoeial sieves. Metallic wires should have
Uniform diameters,
Strength to tolerate mechanical pressure without distortion,
should not have coating or plating. and
No reaction between the materials to be sieved and the metal used to make
Standard of sieves:
Pharmacopoeial Sieves must specify the following information
1. Sieve Number: The number of mesh in 25.4 mm (1 inch) in each direction parallel to the wire is the sieve number. For example, Sieve number 22 will have 22 mesh in the 25.1 mm2 area of the sieve. Sieve number 44 will have 44 meshes in 25.1 mm2 area of sieve. Thus sieve number 22 will have a larger mesh than sieve number 44. As the sieve number increases there will be a decrease in mesh size.
2. Normal aperture size: It represents the size of the mesh square aperture of the sieve. It is the distance between two adjacent wires. It is measured in cm or mm or micrometer (µm).
3. Nominal diameter of wire: Specified diameter of wire to provide specified mesh aperture size with sufficient strength to maintain sieve and sieve aperture size.
4. Approximate percentage area of sieve: It is an area of mesh that occupies the total area of the sieve. It is decided by the diameter of the sieve wire. Normally sieve area ranges from 35% to 40%. This range of percentage area is sufficient to provide the required strength to the sieve.
5. Tolerance average aperture size: Ideally mesh size of the sieve should be of uniform size. But practically, it is not possible. Variation in the mesh size of the sieve is expressed as the “aperture tolerance average” It is expressed in percentage. Pharmacopeia specifies some limits in this variation of aperture size. The aperture tolerance average is on the lower side for coarse sieves while it is higher side for fine sieves. Fine meshes cannot be woven as accurately as coarse meshes.
Types of Sieves
The following types of sieves are used in the pharmaceutical industry.
1. Woven wire sieves: It is made up of metal wires. The weaving pattern may be a plain weave or a twilled weave. These sieves are most widely used in pharmaceutical industries as hand sieves or in mills like ball mills, roller mills, etc.
2. Bolting cloth sieves: Twisted multi-strand fibers of silk or nylon are used in bolting cloth sieves. They are suitable for fine powders.
3. Bar screens: These are made of cross bars fixed parallel. Clogging or blocking of sieve mesh does not occur during sieving. They are suitable for handling heavy pieces of materials such as in mining.
4. Perforated screens: It is made up of metal sheets with round, oval, square, or rectangular holes. Plates with a small number of holes shall be stronger than plates with a large number of holes. The perforated screen containing holes inclined at 45 degrees in the plate is a Herringbone design. Perforated plate containing vertical holes (90 degrees or right angle) is Cross cross-slot screen design. Perforated screens are used in the hammer. Herringbone design is suitable for screening amorphous and crystalline materials. It is not suitable for fibrous materials. Cross cross-slot screen design is suitable for slurries and coarse powder of amorphous materials. It is not suitable for fine grinding because it clogs quickly with the fine particles of powder.
Sieves and standard of sieves: “Pharmacopoeial sieves have a square mesh of uniform size made up of rust-proof metallic wires as woven material.” Normally, metallic wires of brass, bronze, or stainless steel are used in pharmacopoeial sieves.
Classification of powders as per IP:
It is also called the official standard of powder as per IP. Indian pharmacopeia (IP) expresses the degree of coarseness or fineness of powder depending upon the size of the mesh aperture through which powder particles can pass. There are five categories of powders as per IP. IP specifies powder particle size either in mm or µm..7 mm is equal to 1700 µm.
1. Coarse powder (10/44): All particles of powder pass through sieve number 10 (1.7 mm mesh size) and not more than 40% of powder particles pass through sieve number 44 (355 µm mesh).
2. Moderately coarse powder (22/60): All powder particles pass through sieve number 22 (710 µm mesh) and not more than 40% pass through sieve number 60 (250 µm mesh)
3. Moderately fine powder (44/85): All powder particles pass through sieve number 44 (355 µm mesh) and not more than 40% pass through sieve number 85 (180 µm mesh).
4. Fine powder (85): All powder particles pass through sieve number 85.
5. Very fine powder (120): All powder particles pass through sieve number 120.
It is difficult to have all powder particles of uniform size. Hence, IP prescribes two sieve numbers that are, one upper limit and one lower limit for three categories of powders. These powders are coarse powder, moderately coarse powder, and moderately fine powder. The last two categories of powder come under fine powder grade. These fine powder and very fine powder. IP prescribes only one sieve number just to maintain the fineness and quality of the product.
Alok Bains
Methods of size separation
There are four methods to separate powder particles after size reduction. These are Sieving, Cyclone separator, air separator, and elutrition. Here we will discuss only the cyclone separator in detail as prescribed in the syllabus.
Sieving: Powder particles are passed through a series of sieves for their size separation. Sieves are arranged in a sieving machine in descending order. That is the larger sieve at the top and the smallest one at the bottom. The sieve machine separates powder particles by using shaking sieves (agitation), brushing powder bed on sieves, or using gyration (centrifugation).
Air separation: Rotating discs or blades are used to create cyclones inside. The speed of discs or blades decides the size of particles to be separated.
Elutrition: It is used for the size separation of insoluble solid particles present in the liquid. It separates solid particles by using their weight and gravitational force.
Cyclone Separator
Cyclone separator
Principle:
The principle of a cyclone separator is based on the centrifugal force acting on particles suspended in a fluid. It utilizes gravity, centrifugal force, vortex, powder particle density, and cyclone velocity inside the cyclone separator. Cyclone separator separates powder particles into two parts one part has coarse particles and the other part has fine particles.
1. Inlet: The mixture of particles and fluid enters the cyclone separator through the inlet at high velocity. This creates a swirling motion within the cyclone separator.
2. Centrifugal force: Centrifugal force causes the heavier particles to move towards the outer wall of the cyclone. This force is generated due to the inertia of the particles trying to resist the change in direction imposed by the swirling motion.
3. Gravity Separation: Gravity pulls particles downward.
4. Lighter particles and gas continue to move upwards and coarse particles downward.
Construction:
A cyclone separator is a device used to separate particles from a fluid stream based on their size and density differences. The following are the basic construction of a cyclone separator:
1. Cylindrical body: The main structure of the cyclone separator is a cylindrical body. This body is made of metal, plastic, or fiberglass and is shaped like a cone, narrowing towards the bottom.
2. Inlet: The fluid stream containing the powder particles enters the cyclone separator through an inlet located tangentially at the top of the cylindrical body. This tangential entry creates a swirling motion within the cyclone, known as cyclonic motion.
3. Outlet: At the top of the cyclone separator, there is an outlet for the clean fluid to exit. Since the heavier particles are forced towards the outer wall, they move downward toward the bottom of the cyclone.
4. Bottom Outlet: At the bottom of the cyclone separator, there is an outlet for the heavier particles.
5. Dust Collector: A dust collector is attached to the bottom outlet to collect the separated particles. This collector prevents the particles from re-entering the fluid stream.
6. Air Lock Valve: In some designs of cyclone separators, an airlock valve may be included at the bottom outlet to allow continuous discharge of separated particles without allowing air or fluid escape.
7. Support Structure: The cyclone separator is mounted on a support structure to keep it stable and positioned correctly.
Working:
A cyclone separator is a device used to separate solid particles from a fluid stream based on their size and density differences. It works on the principle of centrifugal force. The following steps are followed:
1. Inlet: The fluid stream containing solid particles enters the cyclone separator through an inlet nozzle tangentially to create a cyclone.
2. Acceleration: This tangential entry creates a swirling/spiral motion within the cyclone. Spiral motion is due to centrifugal force and tangential entry of fluid.
3. Separation: The centrifugal force causes the solid particles to move downwards along the outer wall of the cyclone while the lighter gas or liquid continues to move upwards towards the center.
4. Collection: The separated solid particles, being heavier, spiral downwards and collect at the bottom of the cyclone separator.
5. Clean fluid outlet: The fluid and fine particles exit the cyclone separator through an outlet located at the top center. Solid particles are collected in the bag and clean fluid exits from the cyclone separator. of the cyclone.
Main factors
1. Design Parameters: The design parameters decide the efficiency of a cyclone separator. It includes the diameter of the cyclone, the inlet velocity, the particle size distribution, and the shape of the cyclone.
2. Efficiency: Cyclone separators are efficient for separating relatively large particles (> 5 micrometers). They are commonly used as pre-filters to remove coarse particles before finer filtration processes.
3. Maintenance: Cyclone separators generally require low maintenance compared to other separation devices due to their simple design and lack of moving parts. However, they may need periodic cleaning to prevent buildup of collected material.
Advantages:
1. High Efficiency: Cyclone separators are highly efficiency in separating powder particles from air or gas streams. which utilizes centrifugal force.
2. Low Maintenance: They have relatively simple designs with no moving parts. It requires low maintenance.
3. Compact Size: Cyclone separators are compact in design. It is to be installed in a limited space.
4. Cost-effective: They are cost-effective compared to other types of powder particle separation equipment, both in terms of initial investment and operational costs.
5. Robustness: Cyclone separators are robust and can handle abrasive materials without significant wear and tear.
6. Versatility: They can be used for a wide range of applications.
Disadvantages:
1. Limited Particle Size Range: Cyclone separators are effective for larger particle sizes but may not be as efficient for very fine particles.
2. Pressure Drop: They can cause a pressure drop in the system, which may require additional energy consumption to overcome, especially in high-flow applications.
3. Collection Efficiency: While cyclone separators are generally efficient, they may not achieve the same level of particle collection as more complex separation methods, especially for finer particles.
4. Particle Re-entrainment: Particles that have been separated re-enter the gas stream, reducing overall efficiency.
5. Sensitivity to Operating Condition: Cyclone separators may be sensitive to changes in operating conditions such as flow rate, pressure, and particle characteristics, which can affect their performance.
6. Space Requirement: They are generally compact, However, larger cyclone separators may still require significant space for installation, which could be a limitation in certain environments.
Applications:
To separate solid particles from gas or air
b. To separate powders depending upon powder particle size.
c. To separate coarse particles of powder and fine particles of powder
d. To separate solids in liquid suspension
Alok Bains
B.
C. Working: Mixture of powder particles in air or gas enters at very high speed into cyclone separator through the tangential inlet. Air will flow and develop rotary motion inside a vertical cylinder. Solid particles under centrifugal force and vortexing force rotate inside the vessel. Solid particles larger in size and heavy in density shall be thrown out towards the wall of the vessel. These particles fall to conical bases as velocity decreases. They are collected at the bottom of the vessel. Smaller particles with low density move out through the air outlet at the top of the vessel.
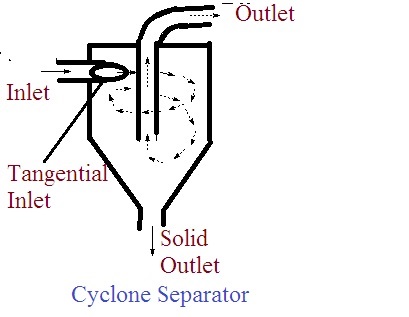
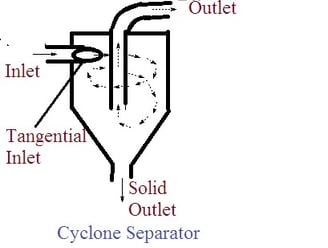