Size Reduction
Size Reduction: Definition, Objectives/Applications, Principles, Construction, and Workings of Hammer mill and Ball mill
PHARMACEUTICS
Alok Bains
10/17/20235 min read
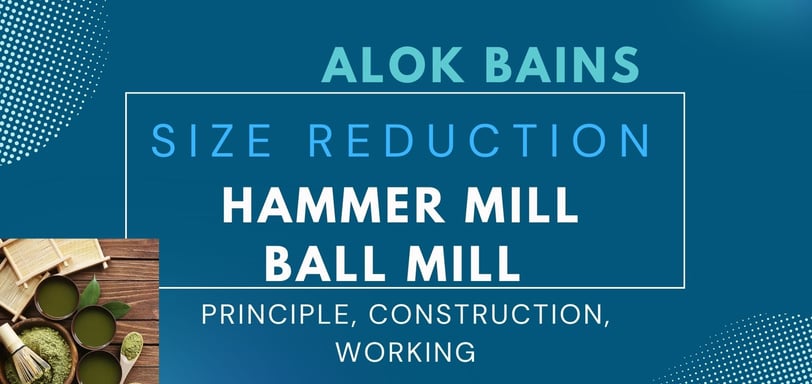
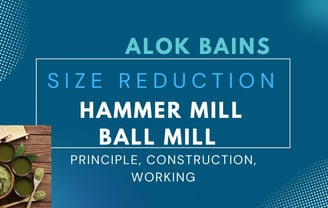
Size Reduction: Definition, Objectives/Applications, Principles, Construction, and Workings of Hammer mill and Ball mill
Size Reduction (Comminution or Grinding or Milling)
"Size reduction is a mechanical procedure to break solid drug (crude drugs or chemical drugs) particles into smaller pieces, coarse particles, or fine particles". It includes various techniques such as smiling, grinding, and micronization.
Objectives/Application/Importance of Size Reduction
Size reduction is commonly used for the following reasons
Uniformity: Size reduction helps in the uniform mixing of drugs and excipients during the preparation of pharmaceutical formulation.
Increased solvent penetration: An increase in the surface increases the penetration of liquid into drug particles.
Enhanced solubility: Reduction in particle size increases the surface area of drug particles. An increase in surface area increases the solubility of the poorly soluble drugs. This is due to an increase in the contact area between solvent and drug particles.
Increased rate of absorption: An increase in the solubility of drugs increases their rate of absorption from the site of their application.
Increased bioavailability: An increase in the absorption of drugs from the site of application increases the bioavailability of drugs.
Improved dispersion: Fine particles are easier to disperse in liquid formulations such as suspension, syrup, etc.
Improved stability: Size reduction increases the stability of formulations like suspension by slowing the rate of the solid particles' sedimentation.
Factors Affecting Size Reduction
The following factors affect the process of size reduction
Hardness: Soft materials size reduction is easier than hard materials.
Toughness: It is difficult to reduce the size of tough drugs such as fibrous crude drugs. It is more difficult to reduce the size of soft and tough drugs than hard and brittle drugs. Glass is a tough and brittle substance. Rubber is a soft and tough substance. It is easy to reduce the size of glass than rubber.
Stickiness: It is difficult to reduce the size of sticky drugs.
Material structure: It is easier to reduce the size of minerals than vegetable drugs. Minerals have lines of weakness. While vegetable drugs are fibrous.
Moisture: Moisture influences the hardness, toughness, and stickiness of drugs. It is difficult to reduce the particle size of drugs containing moisture.
Softening temperature: Some drugs become soft after an increase in temperature. Their size reduction shall be difficult at increased temperatures such as wax, stearic acid, drugs containing oil/lipid, etc.
Purity required:
Physiological effect: Some drugs are toxic. Their dust during size reduction affects the operator operating the size reduction mill. Their size reduction is carried out in an enclosed mill.
Feed product size ratio: Feed size and product size ratio should be fair. If there is a wide gap, it requires various steps of size reduction such as crushing the drug to form coarse particles. Then coarse particle size is reduced to fine particle size.
Bulk density: The efficiency of the mill depends upon the bulk density of the drug.
Mechanism/Principle of Size Reduction
The following are the Mechanism/Principle of size reduction
Cutting: The particle size of a solid drug is reduced by using a sharp knife blade, root cutter, or any sharp instrument. It reduces the size into smaller pieces. It utilizes shear force to reduce size. An example of a machine is a cutter mill.
Compression: The particle size of the solid drug is reduced by applying pressure at a time on the upper surface and lower surface of the particles. It crushes the particles into smaller sizes by using compression force. Examples are motor and pestle in a laboratory. Roller mill for large-scale size reduction.
Impact: Collision of a rapidly moving object with a stationary object generates high energy impact. This breaks the particles of one object into smaller particles by using impact force. Examples are hammer mill and disintegrator
Attrition: The application of both compression force and friction on particles between two surfaces is called attrition. It reduces the size of particles by using compression and friction. Examples are ball mill and fluid energy mill.
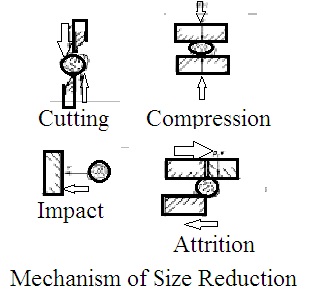
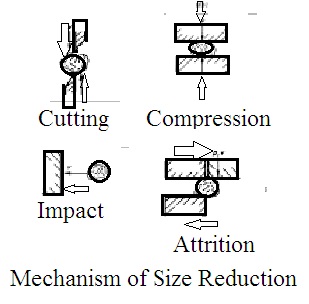
Hammer mill
Principle: It works on an impact mechanism. One object moves against a stationary mechanism. The hammer inside the hammer mill moves at a very high speed against more or less stationary materials inside the hammer mill.
Construction: It consists of a metal body. The metal body has a hopper to feed materials (feed inlet) inside the hammer mill. The metal body encloses a central shaft and four or more swinging hammers attached to the shaft. The hammer mill has also an electric motor to rotate the shaft and hammers at the central axis of the shaft. The lower part of the metal body has a sieve screen for the product outlet.
Working: Put the material into the hopper of the hammer mill. Rotate the shaft and hammers at high speed by using an electric motor. The hammer hit the materials to generate impact. Materials thrown out that strike with the stationary wall of the hammer mill and move back to strike the rotating hammer. This generates an impact to reduce the size of the particles. Size reduction occurs inside the hammer mill. Reduced particles come out from the hammer mill through the screen sieve.
Advantages: Hammer mill is a continuous process. There is a low chance of jamming the hammer mill during operation. It produces moderately fine powder.
Disadvantages: The high-speed rotation of the hammers generates heat. Thus it is not suitable for thermolabile materials. Foreign hard materials in the feed may damage the hammer during operation.
Uses: It is used to produce moderately fine powders of materials except sticky materials.
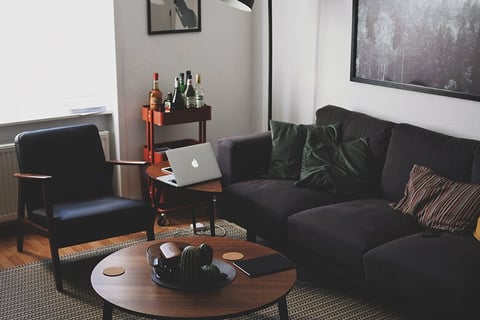
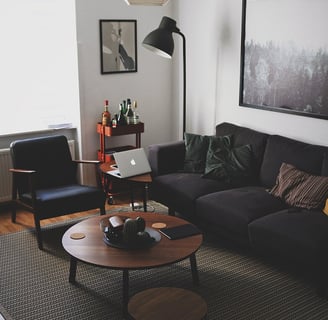
Ball Mill
Principle: It works on a combination of two mechanisms attrition and impact.
Construction: It consists of a hollow metallic cylinder mounted on a metallic frame. The hollow metal cylinder rotates at the horizontal axis. The ball mill is attached to the electric motor to rotate the hollow metallic cylinder. The hollow metallic cylinder has small balls of various sizes that occupy 30 to 50 % volume of the metal cylinder. The size of the balls depends upon the diameter of the metal cylinder. Normally balls are made of metals. Balls lined with chrome, rubber, or porcelain are also available for the ball mill.
Working: Put the material into the metal cylinder of the ball mill. Rotate the cylinder by using an electric motor at the horizontal axis. The speed of rotation is very critical. At low speeds balls and materials will slide with the wall or roll over each other. There will be negligible size reduction. At high speeds, the ball and materials will stick to the wall of the metal cylinder due to centrifugation forces. There will be no size reduction. A speed of about 70% of the speed that generates centrifugation force is critical speed for the size reduction of the materials. At this speed, balls will move with the wall of cylinder metal up to the top and then fall in. Falling balls generate an impact on the materials for size reduction. During the movement of balls with the cylinder wall, balls will roll over each other. Size reduction of materials occur during this rolling by attrition force.
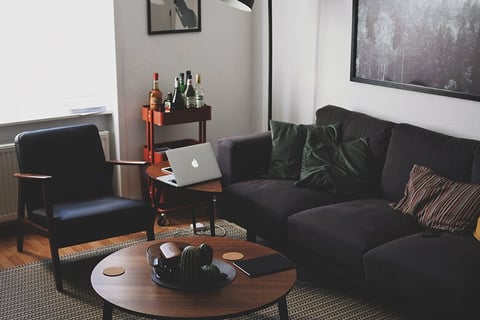
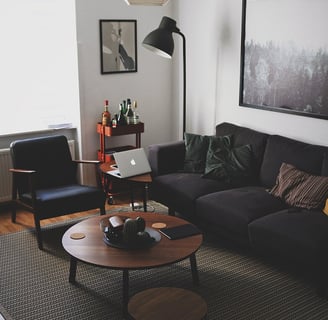
Uses: A ball mill is used to grind brittle materials to fine powder.
Advantages:
Produce very fine powders
Continuous process, if a seven is attached to the metallic cylinder
Grind a very large variety of materials
Suitable for both dry grinding and wet grinding
Useful for toxic materials as it is an enclosed mill if sieves are not attached.
Disadvantages:
Noisy machine
Ball particles come out from balls during size reduction. This contaminates materials during size reduction.
Alok Bains