Drying
Drying: Definition, Objectives, Applications, Principle, Construction, Working of Fluidized Bed Dryer, Freeze Drying
PHARMACEUTICS
Alok Bains
11/4/20239 min read
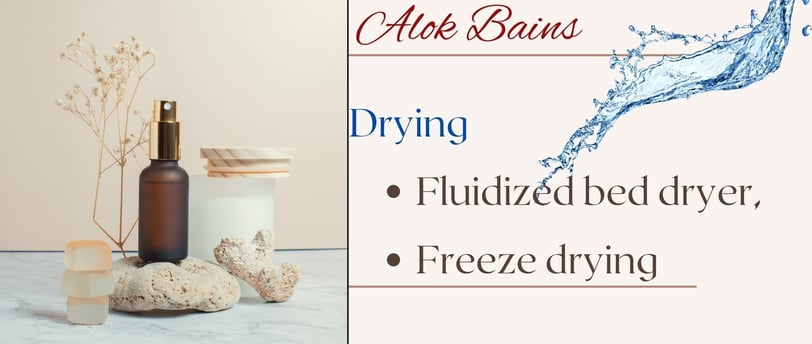
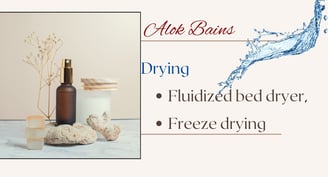
Drying: Definition, Objectives, Applications, Principle, Construction, Working of Fluidized Bed Dryer, Freeze Drying.
Drying: Definition, objectives, applications, principle.
Drying is the unit operation to remove water or moisture from the solid to the external atmosphere by exposing it to air, heat, or drying agents.
Objectives of drying
To make solid products free from moisture to enhance their stability and shelf life.
Applications:
1. Drug formulations: To remove moisture from active pharmaceutical agents and excipients during formulations of various solid dosage forms. Such as
a. Powders: Drying powders' ingredient increases their free-flowing properties stabilizes all ingredients and decreases susceptibility to bacterial growth.
b. Granules: Drying of granules increases their free-flowing properties stabilizes all ingredients and decreases susceptibility to bacterial growth. This controls weight variations in tablets and capsules.
c. Size reduction: Drying facilitates size reduction of solids and crude drugs
d. Reduce bulk weight: Drying reduces the bulk weight of dosage form which will facilitate easy transportation and dispensing of solid dosage form.
2. Preservation: Removal of moisture helps to preserve the crude drugs by blocking or slowing their hydrolysis and oxidation. Dried products are more stable than moist products.
3. Shelf life: Drying preserves crude drugs and solid dosage forms from hydrolysis and oxidation. This increases the shelf life of medicaments.
4. Powder production: Drying helps to recover solids present in solution or suspension.
5. Analytical testing: Various analytical testing instruments require moisture-free products to be analyzed. For example, infrared spectroscopy analysis, X-ray diffraction, etc.
6. Sterilization: The hot air sterilization method sterilizes products utilizing drying techniques.
Theory of drying
Drying requires both heat transfer and mass transfer operations. Both govern the movement of moisture from the surface of the material to the surrounding environment.
1. Heat transfer: There shall be one source to provide latent heat of vaporization. There are three modes to transfer heat from the source of heat of vaporization to the solid. These are conduction, convection, and radiation.
a. Conduction: Transfer of heat from one molecule to another molecule of solid from higher temperature to lower temperature. This occurs in substances which are in direct contact with each other. This provides heat to water molecules present inside solids.
b. Convection: Transfer of heat from one molecule to another molecule in liquid.
c. Radiation: Transfer of heat from one body to another body without using any medium.
2. Mass transfer: There shall be another source to transfer vapor from the surface of the solid into the external atmosphere. During drying a layer of liquid develops at the surface of the solid. It utilizes the heat of vaporization through conduction, convection, or radiation. Moisture comes out from the surface as vapor into the external atmosphere. The rate of this removal shall depend upon the difference in humidity at the surface of the solid and in the external atmosphere of the solid.
The rate of drying can be increased by increasing the rate of heat transfer and mass transfer. The rate of heat transfer shall depend upon the temperature difference between molecules in a solid body. The rate of drying can be increased by using the following factors:
· Convection heat transfer: The rate of convection heat transfer can be increased by increasing the airflow rate and inlet air flow rate.
Radiation heat transfer: The rate of radiation heat transfer can be increased by installing a radiation source inside the drying chamber.
· Conduction heat transfer: The rate of conduction heat transfer can be increased by reducing the thickness of dried materials. The increase in the contact area between the heat source and the solids to be dried also increases the rate of conduction heat transfer.
· Mass transfer: The rate of mass transfer of vapor from the surface of a solid can be increased by increasing the velocity of air
· Dehumidifier: A dehumidifier attached to the drying chamber removes the vapor from the external environment of the solid. This will create a humidity differential. This will increase the rate of mass transfer.
Alok Bains
Fluidized bed dryer
Drug particles or drug granules are dried bypassing hot air or hot gas through a bed of drug particles or drug granules. Drug particles or granules are dried while suspended in the air.
Objectives
1. Drying: To remove moisture from the solid particles or granules.
2. Uniform drying: To provide uniform and rapid drying of all particles and granules
3. Rapid drying: To provide quick and efficient drying to increase productivity.
4. Improved quality: To improve the quality of dried product by providing gentle heating to avoid overheating.
5. Energy efficiency: To provide quick heat transfer through conduction or radiation and quick mass transfer of water molecules to save energy and time.
6. Low contamination: To dry solids inside a closed chamber and use hot clean air or gas to avoid any contamination.
Principle
Hot air/gas passes through the bottom of the bed of the solid particles. Hot air or gas blows at speed to move solid particles in an upward direction. The velocity of the solid particle's movement in an upward direction shall be slightly higher than its downward settling velocity. This leads to suspending solid particles in the air and creates a fluidized bed of solid particles/granules. A Mixture of Solid particles or granules and air inside the chamber behaves like a fluid. Thus it is called a fluidized bed dryer.
Hot air or gas surrounds each solid particle or granule. This leads to
1. Quick heat transfer to each particle or granule from hot air or gas and
2. Quick mass transfer of water molecules from particles or granules into the air.
Water molecules as vapor come out from the fluidized bed dryer decreasing humidity inside the chamber. There shall great difference in the moisture contents in between solid particles or granules and surrounding air or gas.
Quick transfer of heat, quick mass transfer of water molecules, individual particles/granules drying, and moisture difference between solid particles or granules and surrounding air/gas lead to quick-drying, uniform drying, uniform composition, and uniform particle size distribution.
Construction:
There are two types of fluidized bed dryers in the pharmaceutical industry.
1. Vertical fluidized bed dryer: Batch drying
2. Horizontal fluidized bed dryer: Continuous drying.
Vertical fluidized bed dryer is most commonly used. It is made of a stainless steel chamber resistant to corrosion and high temperature with a perforated bottom. Its capacity to dry solid particles/granules may vary from 5 kg to 200 kg. It has the following components
1. Air supply: It consists of a fan or blower to introduce air/gas into the fluidized bed dryer chamber through the air filter, heating system, perforated plate, and solid particles/granules bed.
2. Heating system: It consists of a gas-fired burner, electric heater, or steam heat exchanger to heat air or gases entering into the chamber from an air supply source.
3. Air distributor: It consists of a series of nozzles fitted at the bottom of the perforated plate. It distributes hot air or gas evenly to pass across solid particles or granules bed.
4. Perforated bed: It is made of a perforated plate or wire mesh designed to hold solid particles or granules. It allows hot air or gas to pass from its bottom and through the particle bed.
5. Exhaust: It consists of ducts, an exhaust fan, and a filter bag to remove moist air from the chamber and retain dried solid particles or granules.
6. Control system: It consists of sensors and controllers to control various parameters such as temperature, air flow rate, bed height, exhaust rate, etc.
Working: Load solid particles/granules over the perforated bed inside the fluidized bed dryer chamber. Introduce filtered hot air/gas into the chamber through a perforated plate and solid particles/granules bed. The velocity of air expands the bed. As the velocity of air increases bed expansion will also increase and particles/granules will float inside the chamber. Each particle and granule shall be in direct contact with the hot air/gas. Drying will occur and moist air will be rapidly removed through the exhaust system. Dried particles/granules shall be collected in the dust bag that will settle down on the bottom of the chamber after completion of drying.
Advantages
1. Efficient drying: Each particle/granule floats individually. This increases the surface for drying for heat transfer and mass transfer. Thus rapid rate of drying. It takes 15 to 30 minutes to dry 5 kg to 200 kg solid particles/granules.
2. Uniform temperature: Temperature shall be uniform throughout the chamber to dry floating particles/granules.
3. Uniform drying: Each particle/granule is in close contact with hot air/gas. This leads to uniform drying.
4. Constant rate of drying.
5. Minimum degradation: Less duration to heat exposures. This protects the drug from thermal degradation or damage due to agitation. Suitable for heat-sensitive drugs.
6. Free-flowing product: Uniform drying, complete drying, and uniform particle size distribution lead to the development of the free-flowing characteristics in the product.
7. No migration of chemicals: Individual particles/granules drying stops the migration of chemicals during drying that occurs in the static bed.
8. Economical: Rapid drying leads to time shaving, labor cost shaving, and high output.
9. Less space: The vertical and compact design of the fluidized bed dryer occupies less floor space.
Disadvantages:
1. High initial investment: Expensive to purchase and install the machine.
2. High energy consumption: High energy consumption to operate the machine
3. Particle attrition: Particles collide during floating causing attrition and the formation of fine particles.
4. Dust emission: Generate large amounts of dust particles.
5. Limited capacity: Batch process, thus limited capacity.
6. Product sticky: Difficult to dry sticky materials.
7. Process control: Optimization of machine requires for materials to be dried. It varies from product to product.
FREEZE DRYING
“Removal of water content from frozen materials without melting the ice is called freeze drying.” The Conversion of water from ice to vapor without The formation of a liquid state is called sublimation. Thus freeze drying is also called sublimation drying. Freeze drying is also called lyophilization because The materials to be dried are dissolved in The solvent and then The solvent is removed by sublimation. Lyo means dissolve and Philein means love. It involves two steps freezing and drying.
Objectives: The main objectives of freeze drying are to stabilize products, prevent their degradation, and increase The shelf life of the products.
1. Preservation: To preserve biological products such as vaccines, enzymes, antibiotics etc
2. Long-term storage: To remove moisture to inhibit The growth of microbes and other chemical reactions.
3. Easy transport: Moisture removal by freeze drying makes pharmaceutical products lightweight. It facilitates easy and cost-effective transportation
4. Reconstitution: To improve reconstitution properties in products.
5. Improving solubility: Removal of all water contents makes The product
6. Reducing product size: To make products prone to size reduction.
7. Improve quality: To preserve The texture, flavor, medicinal value, and food value of the product.
Application of freeze drying: In pharmaceutical industries, heat-sensitive pharmaceuticals degrade on exposure to temperature. Water contents of heat-sensitive pharmaceuticals are removed by freeze-drying without damaging their chemical nature. Heat-sensitive pharmaceuticals such as vaccines, antibiotics, hormones, enzymes, vitamins, microorganisms, and several biological drugs are dried by freeze drying to prolong their shelf life and inhibit chemical reactions and microorganism growth.
Principle of freeze-drying
Freeze drying is based on the principle of sublimating frozen water into vapor without going through A liquid state. Freeze drying is based on the theory of the “triple point” of water. The Triple point is a critical point for phase transition at which all three states of the substance (solid, liquid, and vapor) exist in equilibrium. The pressure and temperature at which water exists in all three states solid, liquid, and vapor in equilibrium is called the triple point of water. The triple point for water is 0.01 degrees C and 611.73 Pa (6.11 millibar or 0.006 atmospheres).
Under freeze drying, the material to be dried is frozen inside a vacuum chamber. Temperature is provided just above the triple point below the melting point of water. At this point, the ice sublimates to vapor. A vapor is removed from the chamber using a condenser. This forms dry porous material.
Construction: The freeze dryer has the following four components.
1. A vacuum chamber: It consists of a shelf to hold materials to be dried. The rate of freeze drying can be increased by keeping the gap between materials and condenser as low as possible. An increase in the area of the surface of materials to be dried also increases the rate of freeze drying.
2. A condenser: It consists of a large surface area to condense vapor present inside a vacuum chamber. It is cooled by solid carbon dioxide mixed with ethanol or acetone. The temperature of the condenser must be less than the temperature of the frozen material surface to be freeze-dried.
3. A vacuum source: A vacuum pump is used to create a vacuum inside The chamber of the freeze-dryer.
4. A heat source: Heat for vaporization can be provided by radiation, conduction, or both.
Working: There are five steps for freeze drying of materials. These are
1. Pre-treatment: Concentrate the solution by using a vacuum tray dryer. It reduces freeze-drying times almost by 8 to 10 times
2. Pre-freezing: Put The concentrated solution in a bottle and centrifuge it inside The bottle during its freezing. This centrifugation during freezing increases the surface area for sublimation.
3. Primary drying: Maintain freeze dryer temperature and pressure below triple point for the sublimation of water. Supply heat cautiously to sublimate ice into vapor. Primary drying removes 98 to 99% of water present in the product.
4. Secondary drying: The rest of The moisture is evaporated by a normal vacuum drying process at a temperature of 50 to 60 degrees C.
5. Packing: Pack freeze-dried products carefully to protect them from moisture present in the atmosphere. Freeze-dried product is highly hygroscopic that capture moisture from The atmosphere very quickly. If it is a sterile product carry out packing under aseptic conditions to avoid entry of microbes into The product during its packaging.
Advantages
1. Light in weight and porous product.
2. No hydrolysis of product during drying due to temperature.
3. No oxidation of product during drying due to drying under vacuum (no oxygen presence).
4. More stable dried products than dried products from any other process.
5. No loss of volatile constituents
6. Freeze-dried products properly packed are suitable to be stored at room temperature.
7. Suitable for thermo-labile product drying.
8. Easily maintain sterility during drying.
Disadvantages
1. Expensive and complicated equipment.
2. Very hygroscopic product after freeze-drying
3. Time-taking and slow process.
4. It is used only for those products that cannot be dried by any other method.
Alok Bains